On April 20, the RUET IPE Club hosted a dynamic Technical Workshop on Lean, Six Sigma, and Quality Control—an engaging deep‑dive into industrial process improvement and data‑driven decision‑making in the era of Industry 4.0. The workshop bridged the gap between classroom theory and real-world practice by bringing together graduate students, early‑career engineers, and quality professionals. Under the guidance of Lean Six Sigma Master Black Belt Mohammad Anisur Rahman and Black Belt Md. Jobayer Azad Sohel, both of RSPB’s Operational Excellence team—participants explored how Bangladesh’s manufacturing sector is rapidly evolving from its 2nd‑to‑3rd Revolution roots toward a fully connected, sensor‑driven future.
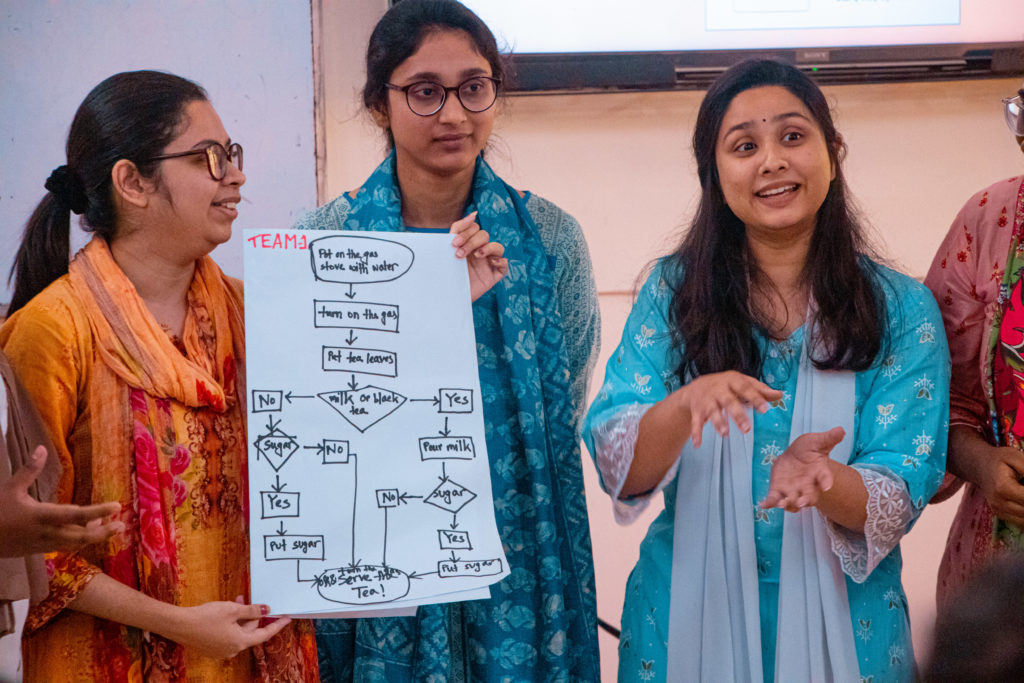
The morning session, “7 QC Tools in Action: Turning Data into Decision,” opened with a discussion of Lean 4.0—an integrated framework that fuses waste‑elimination principles with Industrial Internet of Things (IIoT) technologies and advanced analytics. As industries across Bangladesh continue their transformational journey, the potential gains from streamlined automation and real‑time data capture could not have been clearer. Workshop attendees examined the eight deadly wastes through compelling local examples, then moved on to hands‑on exercises: constructing Pareto charts in Excel and Minitab, drafting Cause & Effect Diagrams to trace PCB failures, and interpreting control charts to pinpoint process variation. By translating raw numbers into actionable insights, participants experienced firsthand how data becomes the cornerstone of continuous improvement.
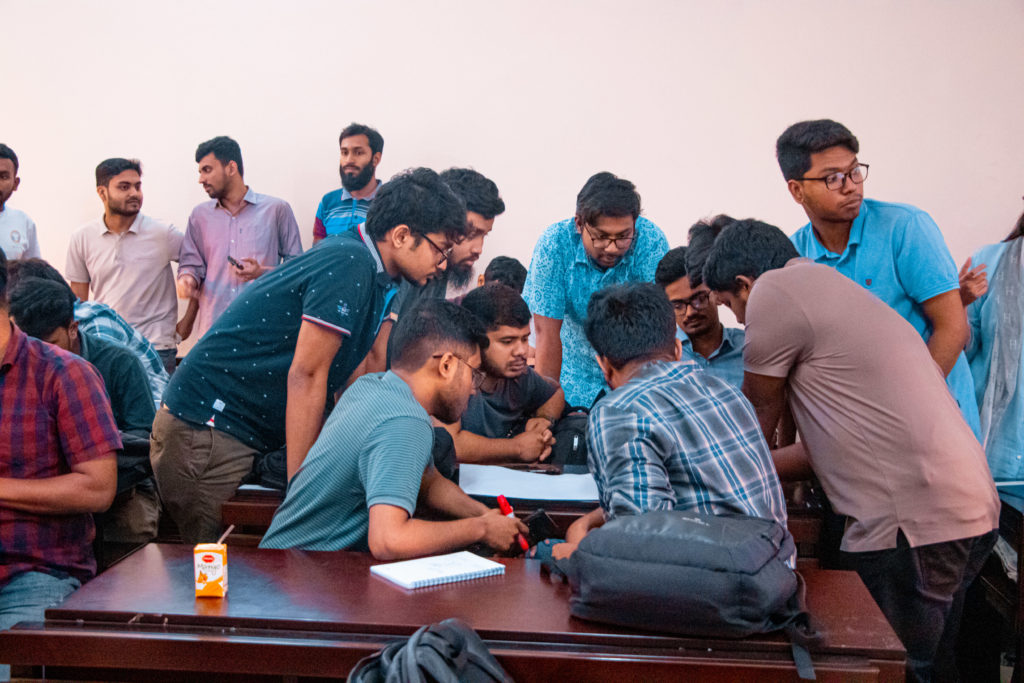
In the afternoon, the “Operational Excellence Reloaded: The Power of Kano and Lean Thinking” session tackled the strategic side of quality management. Through interactive quizzes and games, attendees learned to differentiate internal from external failure costs and calculate the Cost of Quality (COQ) practically. The facilitators introduced the Kano Model, guiding the conversion of Voice of the Customer (VOC) into Critical‑to‑Quality (CTQ) attributes that drive product innovation. A live simulation of a manufacturing and supply chain activity reinforced how standardised IIoT deployments minimise downtime and optimise throughput. By the end of the session, participants confidently mapped customer requirements to process metrics and practised applying lean thinking to real‑world challenges.
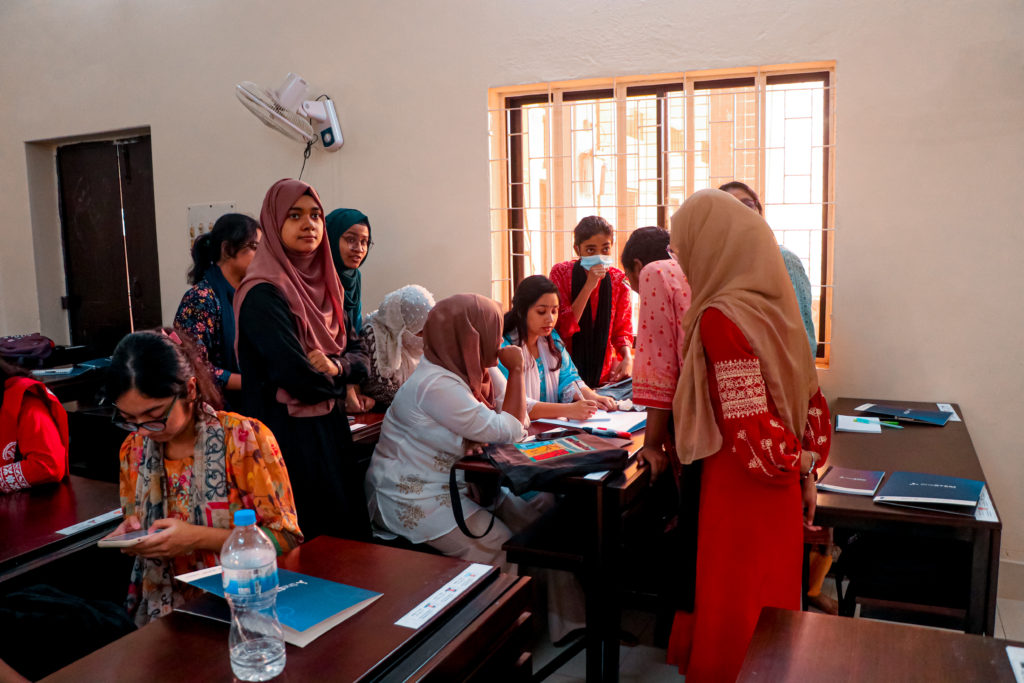
What set this workshop apart was its emphasis on active learning. Rather than passive lectures, every concept was reinforced through problem‑solving exercises—whether analyzing sample datasets in Minitab or collaborating on a root‑cause investigation. The energy in the room was palpable as teams raced to complete quality‑improvement games, debated the priorities on their Pareto charts, and celebrated when their cause‑and‑effect hypotheses held.